
Overview
We are not any type of an NSF certified lab, obviously, and so our experiments and results are going to be imprecise. Before putting any new product on the market, our processes and methods should be reviewed, using more accurate measurement with more standardized methodology.
We are fearless about trying unusual concepts. We are extremely nimble about changing course based on initial test results, and are very persistent at following ideas that appear to make economic sense. We are good at creating new test methods, to quickly evaluate new solutions. We now lead the world in low-cost modification of concrete – to allow it to be pumped into place, yet not needing “forms”. This is an obsession.
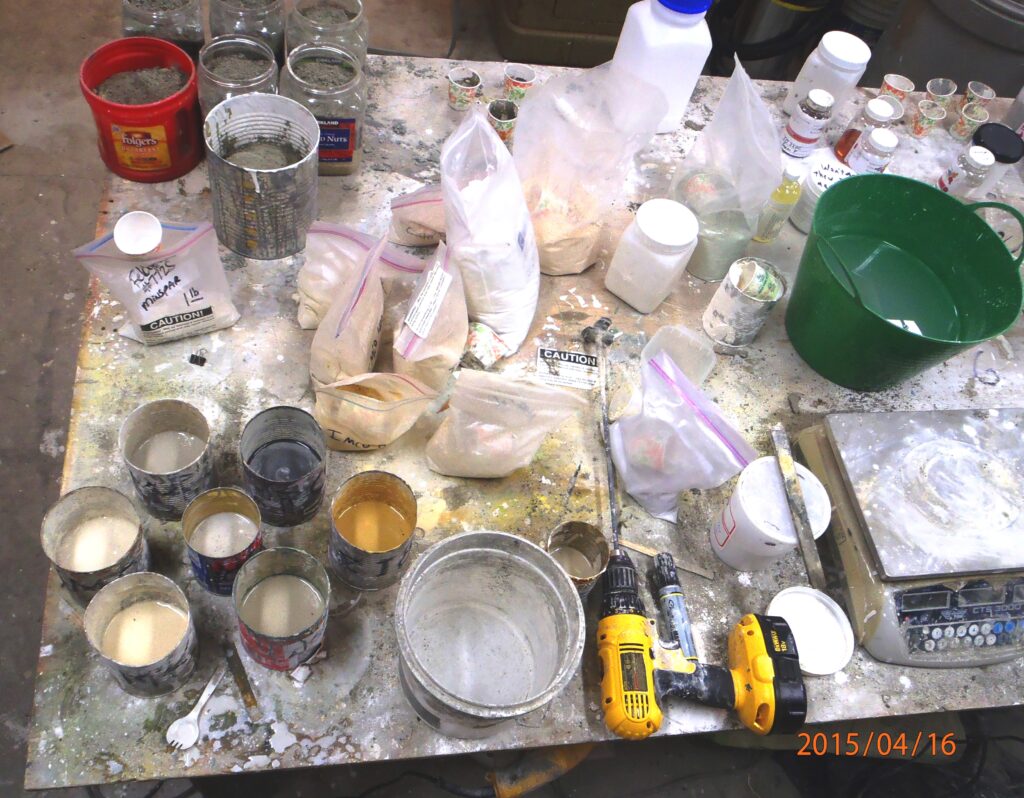
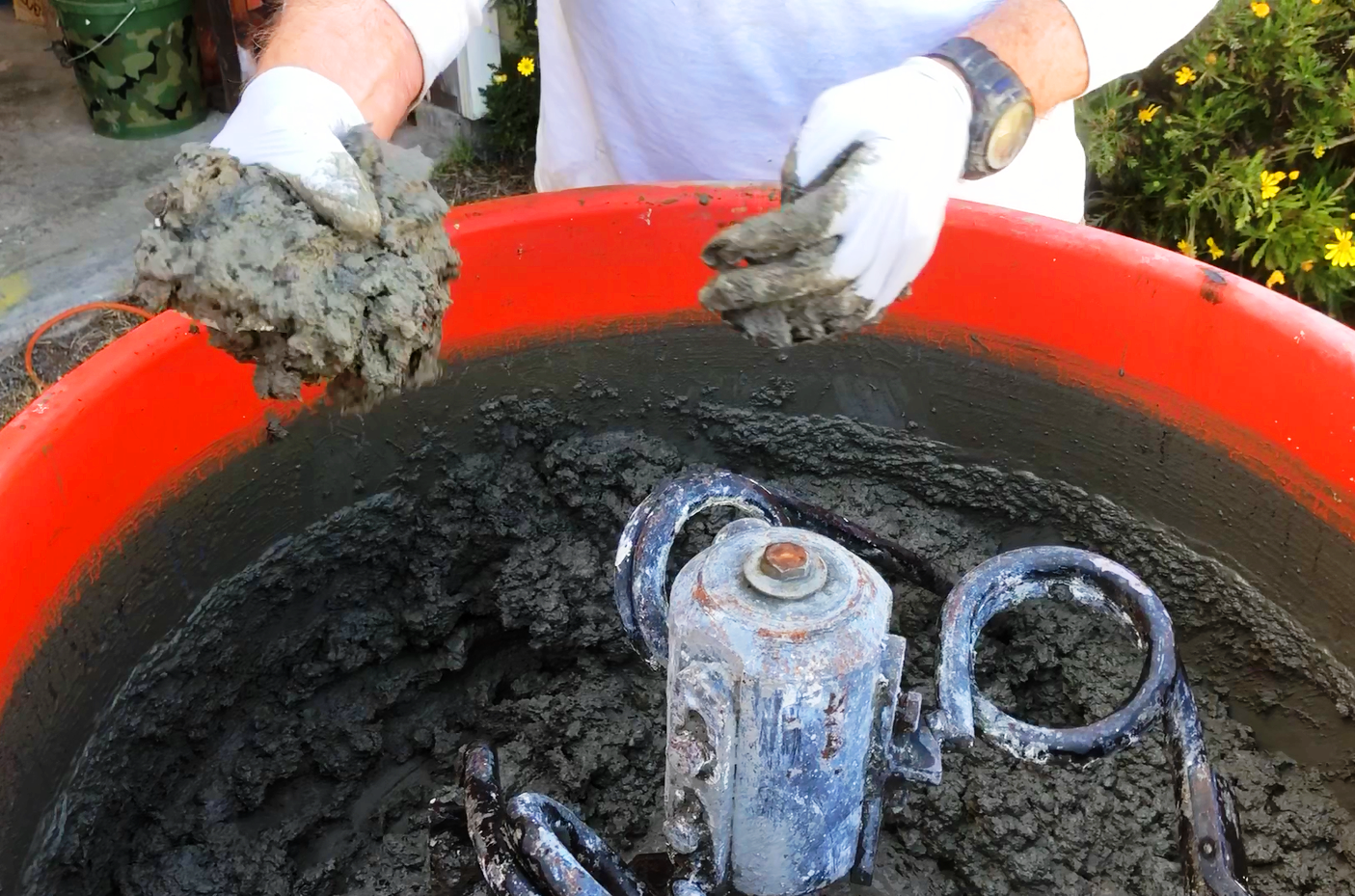
Mix Design
Below is an example of a concrete mix design used with the 3D-admix on a test project. The coarse aggregate is only 3/8” only because of our older ball pump. 3/4” rock works better for vertical buildability. For reliable non-blockage 3/4” rock requires a larger inline mixer than the one we are testing with. The mix water amount may vary, as our local batch plant does not know precisely the moisture content of the sand, etc, on any given day. The 3D-admix dose is highly dependent upon the w/c, and is largely independent on the use of a water reducer. In other words, the actual w/c is what affects the required dose of 3D-admix. Most of the additional slump induced by a water reducer is killed by the 3Dadmix. Most of the testing has been with either no water reducer, or with a PCE-based High Range Water Reducer, so these are what we know the most about at this point.
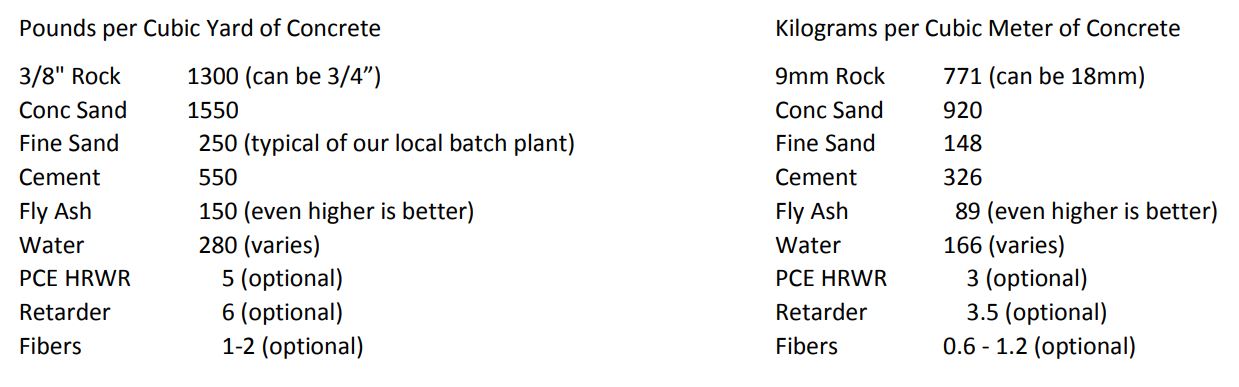
The 3D-Admixtm Concept
It took a while. We figured out how to use a liquid-carrier to reliably deliver inexpensive highly-concentrated basic water-reactive components into concrete. A paint pump can make the fluid injection. The high-solids active-components remain as a stable liquid until entering the aqueous environment of the concrete mix water, where they react in stages, increasingly thickening the concrete, but providing extreme shear thinning – so is very sensitive to vibration. It is like a false set that keeps repeating each time after vibrating it down. In fact, it holds shape better after being vibrated.
Ultrasonic Measurement of Concrete Set
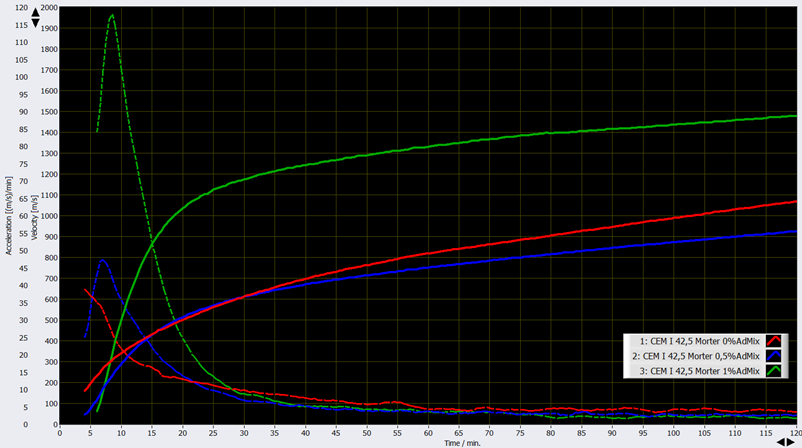
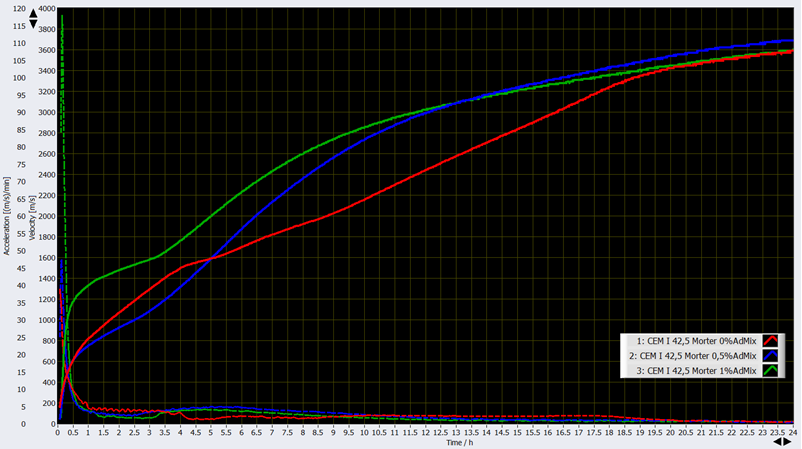
These graphs show the change in set of a mortar (with 8mm coarse aggregate which is really concrete) where 3D-Admix is dosed at 0.5% and 1% of cement (binder). This corresponds to about a ¼ gallon to ½ gallon of 3D-Admix per yard, using the mix design above. The dashed green line shows the “kick” to initial set provided by ½ gallon of 3D-Admix per yard.
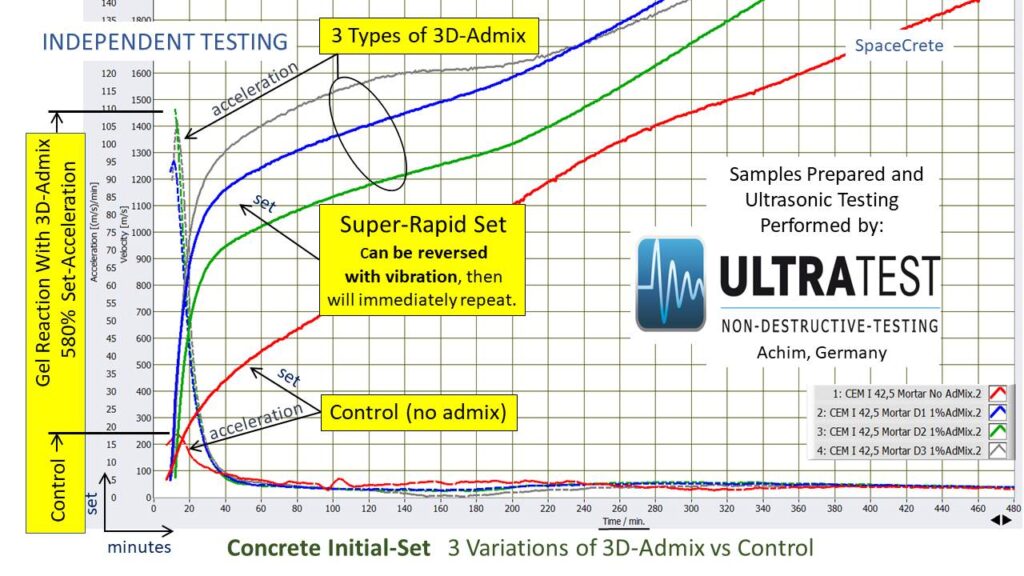
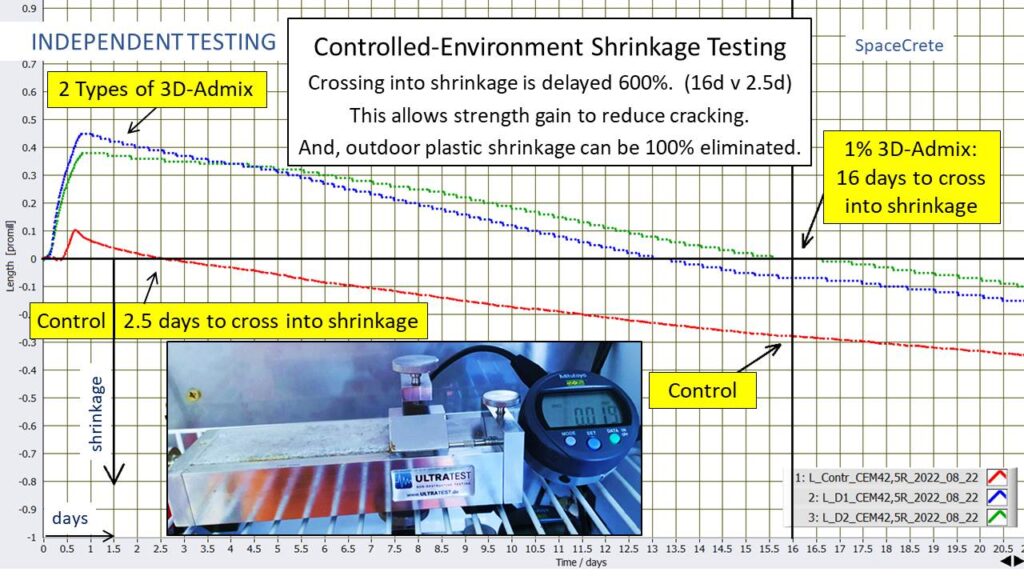
3D-Admixtm Dose
The actual w/c (aggregates at SSD) will determine the necessary inline-injected 3D-admix dose. The 3D-admix dose is very sensitive to w/c, though ironically, we don’t ever really know what the delivered w/c actually is. What we can say is that with the low dose of a PCE HRWR as shown, and an initial slump of 5”, an acceptable dose of (the present) 3D-admix will be around 10 lb per Yard (6 Kg per Cube), or 0.25% of total concrete mass. As the 3D-admix density is around 1.5g/cc, this is 0.37% by volume, or about 80% of a gallon per Yard (or about 4L per Cube) If you were to increase the w/c by 10%, then the 3D-admix dose may need to increase by as much as 50% – it is very sensitive to the available water. Conversely, if you decrease the delivered slump to 2”, or increase the HRWR while maintaining a 5” slump (hard to do), then the ideal admix dose is around 6 lb per yard – which is a half-gallon per yard (2.5L per Cube).
The best method is performance-determined, rather than predetermined ratios; you dose according to how the concrete needs it for the project at hand, keeping in mind that if the concrete has more water, you need to have the extra admix on hand. Not a big deal, as the materials are inexpensive, and the pot life is unlimited (same as the shelf life – which appears to be very long). The ideal dose will also vary with the required vertical build rate. For 3D printing, with the usual very low vertical build rates that are most common, the amount of 3D-admix can actually be significantly lower.
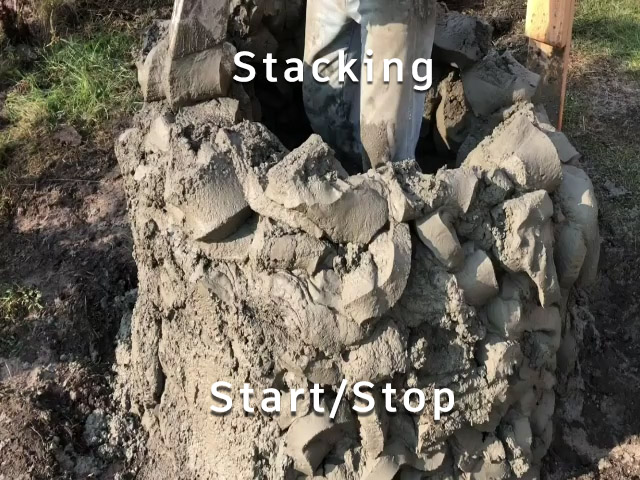
This was normal concrete, pumpable by a
$2500 pump, modified in the pump line.
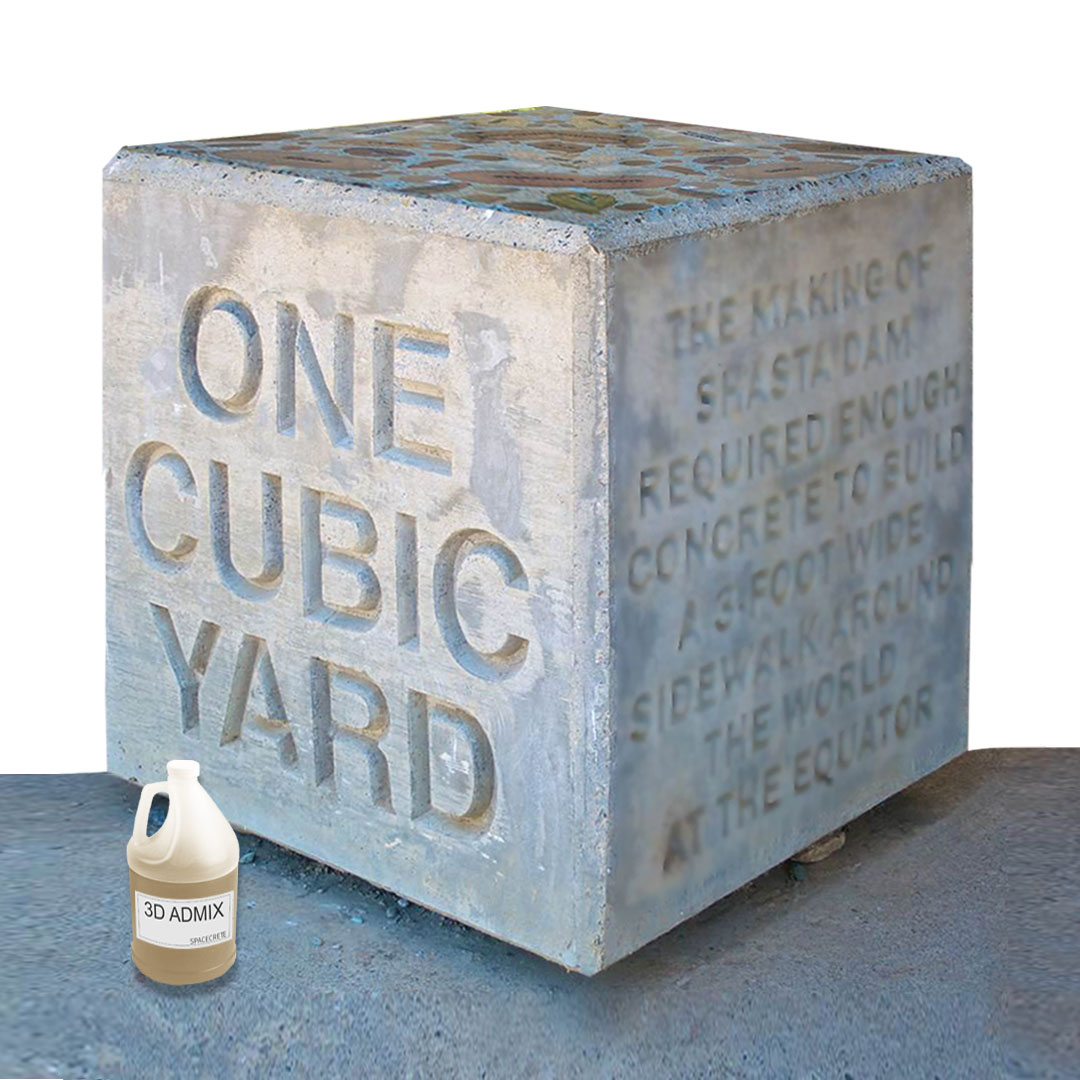
Other variables are involved, such as the use of a retarder to allow the slower deposit rate or for interlayer bonding, or an increased w/c to allow for a lack of vibrational consolidation; and these may bring the 3D-admix dose right back. Of course, the 3D-admix allows a much faster rate of 3D printing than you see being done now.
Why do we proportion the 3D-admix to total concrete and not to the amount of cement? The reason is that the cement content is not that relevant to the proportional dose (while the available water is everything to the dose). The cement proportion does change the 3D-admix dose somewhat, but mostly in the opposite direction. If w/c is held constant, a relatively leaner concrete generally needs more 3D-admix than a relatively richer concrete – within limits, as far as we can tell.
Non-Shrink Effect
The 3D-admix can totally prevent plastic shrinkage, without the use of any SRAs, expensive acrylics or resins, or fibers – even when drying out in the sun. You probably don’t really believe this, and that it totally understandable. But it is true. The higher the dose, the less plastic shrinkage, to zero plastic shrinkage – even in very unfavorable curing conditions. Why is this? It appears to be a combination of the internal curing provided by the cellulose component of the 3D-admix, the very early strength gain of the portland cement because of the 3D-admix, and beneficial effect from the unique liquid-carrier delivery of the active solids. Our 3D-admix testing isolates components to continuously select for shrinkage prevention (favoring low cost materials), and that process has paid off really well.
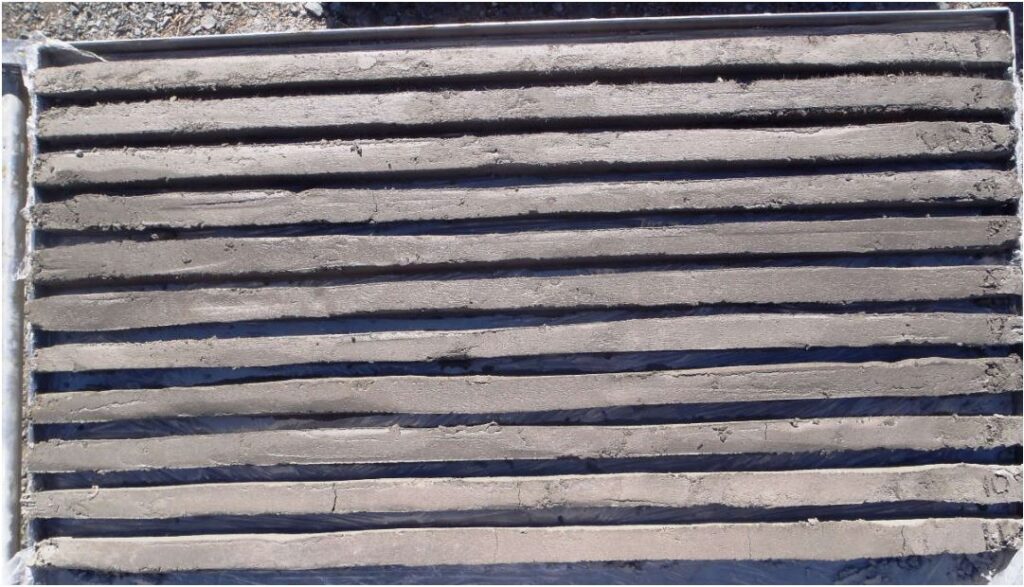
The 3D-admix can also be used as a low-stress delivery mechanism for shrinkage compensators, etc, as these very-fast-setting agents do not set in it – until delivered into concrete. A compensator is not required for prevention of plastic shrinkage, but we do prefer to include one in the 3D-admix, because we just hate cracks. Side-by-side, we found that total shrinkage of SpaceCrete is significantly less than the equivalent unmodified concrete. Most full-scale SpaceCrete test projects have no visible shrinkage cracking, though most of these do have a low dose of fibers (1 lb to 1.5 lb per yard); however the 3D-admix can produce zero plastic shrinkage without any fibers. The associated slabs, using the same concrete, carefully cured, with or without fibers, have all cracked very noticeably. Of course we didn’t put any 3D admix in these horizontal slabs, though now it is looking like a very interesting idea. The 3D-admix material does not cost that much.
In our experience, the inclusion of fibers do not help the vertical build as much as one may think. With use of the 3D-admix, we have found fibers to not make that much difference in vertical build rate. Depending on the fiber type, they really do help concrete robustness and later-term shrinkage, at least. The tradeoff is cost – fibers are expensive. Our view is that it is generally preferable to use a medium-low dose of fibers for walls.
Strength
Early versions of 3D-admix could be very forgiving to work with, but these required a higher dose, and retarded and weakened concrete – issues related to the higher dose and use of surfactants that also increase air content. Much of our plastic shrinkage test of various mineral components in mortar admix R+D has been targeting ways to get rid of the offending components and lowering the dose. We have now done that. More lab testing is needed to be sure, but very preliminary strength testing shows an interesting result: Cored samples of in situ improperly-cured concrete was significantly stronger (even adjusted for age) than the same batch of concrete sampled per the standard test cylinder procedure ASTM C31, that was water-cured in perfect conditions. No fibers were involved. Other types of 3D-print cementitious materials (not SpaceCrete) have shown to be significantly weaker in-situ without proper curing (where it matters), than when cured perfectly in cylinders, as one would expect.
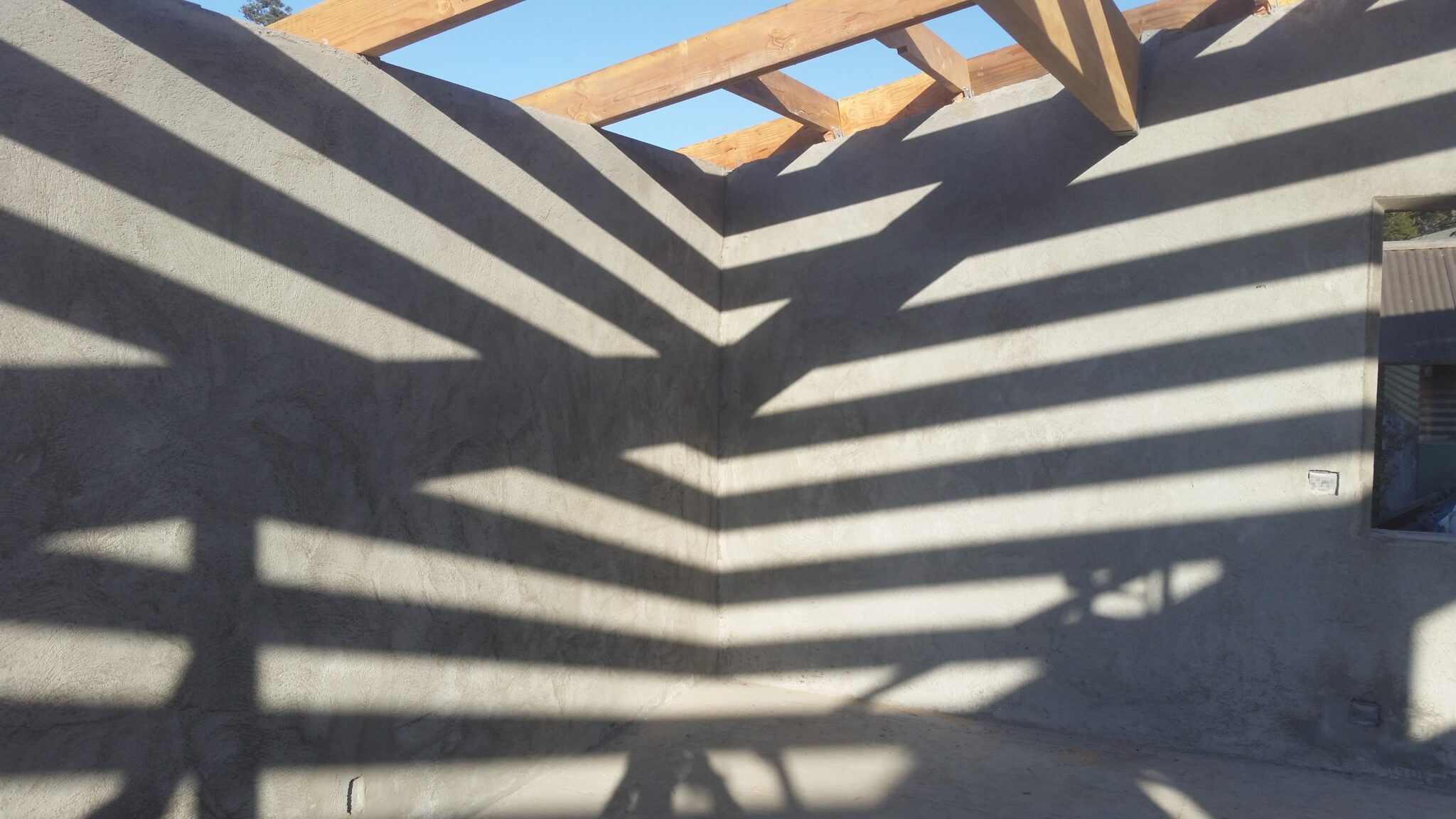
Why would SpaceCrete be the opposite? We think this relates to the internal curing components and related effects of the 3D-admix, along with a delay in developing final strength gain, from other components. The present status is that with a fly ash or no SCM concrete mix, the most recent 3D-admix makes no change to the 28-day concrete strength; but it does seem to weaken a slag concrete mix, and we have no idea why. In any case, a thorough testing regime is warranted, and results should be measured out to at least 56 days, preferably 90 days, to measure subsequent strength gains (or not). Bottom line, there does not seem to be a significant effect from the 3D-admix. In most cases, the design strength of your modified concrete mix design will be the same as what you would get without the 3D-admix.
A Sticky Problem
When you minimize the water in concrete, it will tend to be sticky. A low w/c rich concrete with the 3D-admix is very sticky. It can be challenging to manipulate, place, and tool unless you wet the slip-form or trowel; and when continuously slip forming or autonomously troweling a 3D print, keeping the tool surface wet can be very tricky. This is one of the issues we are working on. Highly stackable concrete also tends to be sticky internally, that is, excessive internal friction and not enough lubricity. There are many solutions, such as replacement nanoclays or surfactants, but these can create other problems, such as increased shrinkage, reduced strength and/or higher cost. Using polymer resins etc. can help, but they are really expensive. One clean cheap strong solution is to just use more fly ash in the mix design. The fly ash does not really help stackability, but it does not really hurt it either, and it really provides lube for a zero-slump mix. A problem arises when your local batch plant can’t get fly ash anymore; so when substituting slag, for example, we find it to be very thirsty and highly frictional. Metakaolin, also thirsty, provides some very nice lube without much shrinkage effect, and helps vertical build, but it is more expensive (batch plants are not going to stock it); still, it is a much better deal than any polymer resin.
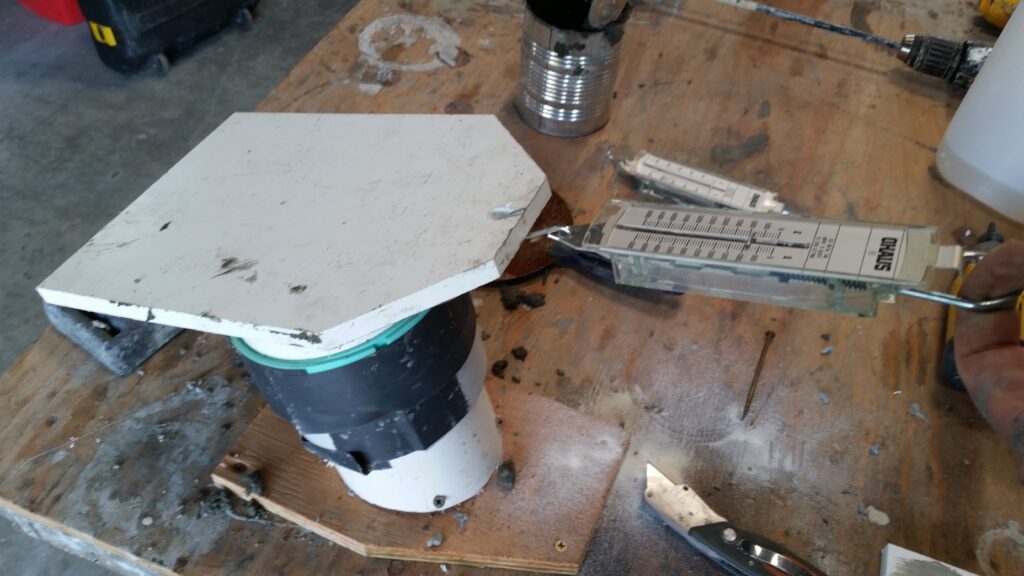
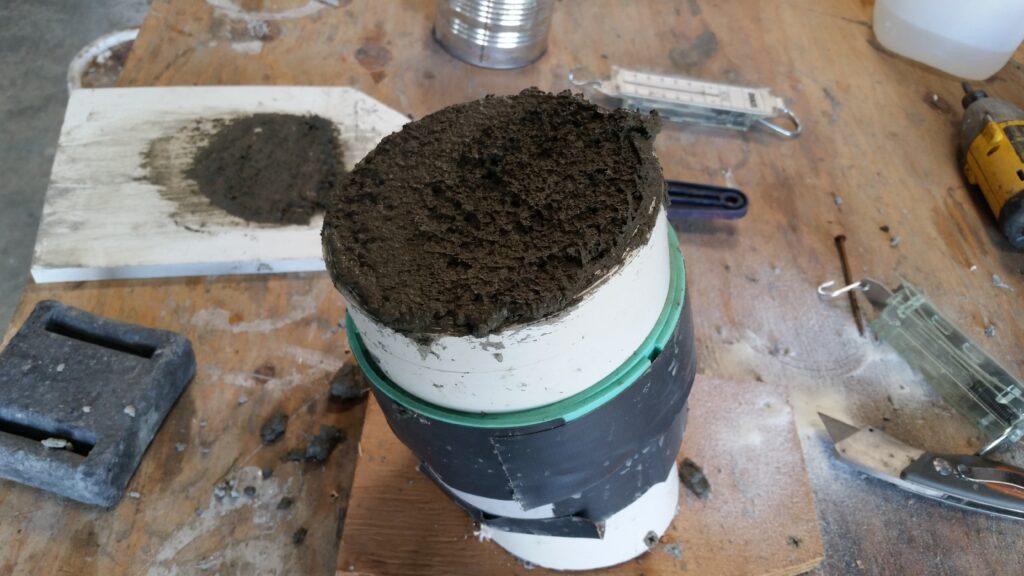
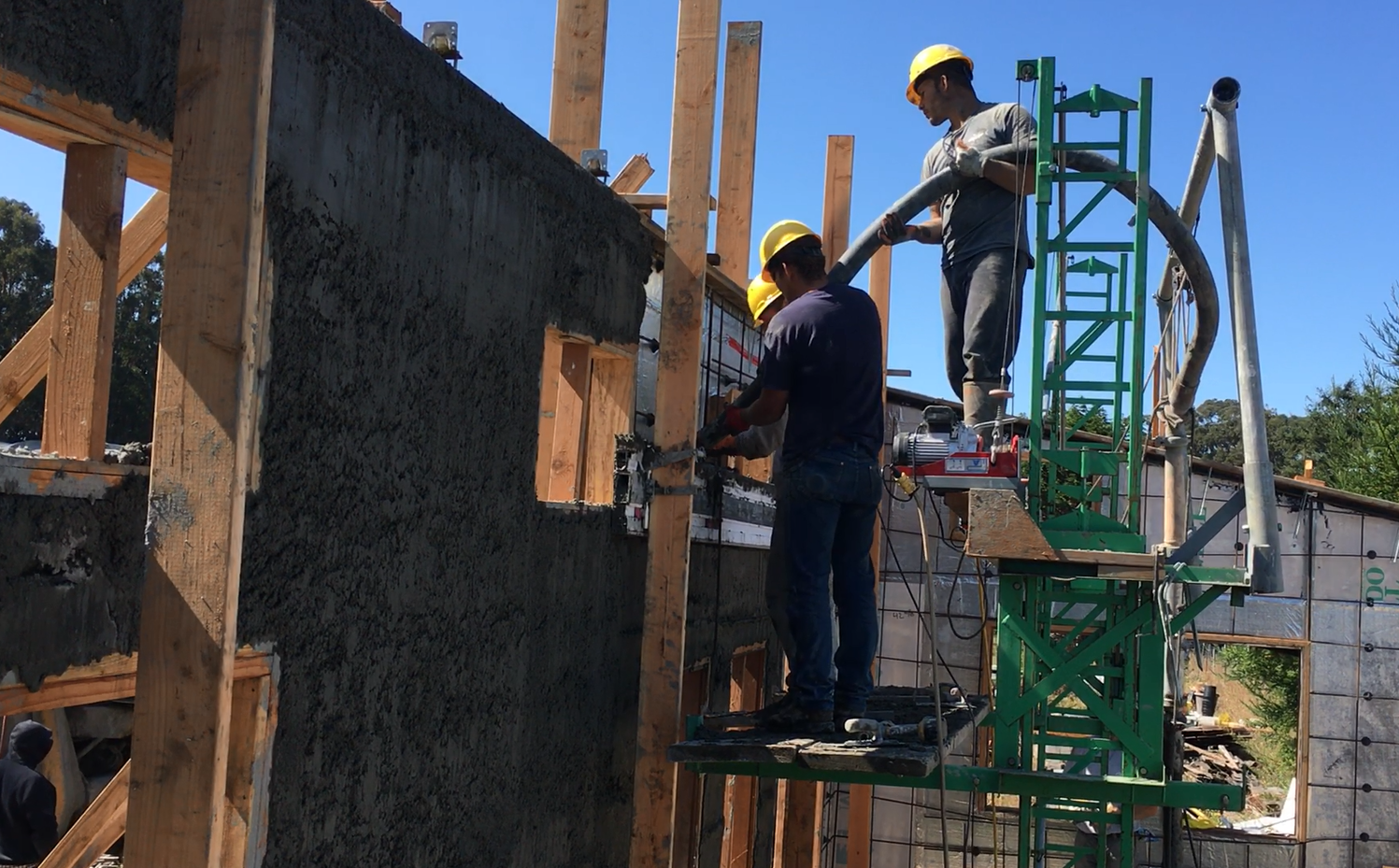
Retarders
We tried a very low dose of retarder (stabilizer) added at the batch plant, and it worked. There was no problem with the build rate, and had the advantage that the concrete in the truck would set up less – giving 3D-AdmixTM dose-effect consistency. So we tried a medium dose, no problem. Then we went with a high dose, where we started in the shade on a cold morning. Too much. The wall build was fine to an 8’ high plate, then it all let go at once. So then we tried really really high doses, to learn the limits of what is possible. We learned that thickening alone – in normal-weight concrete without any cement set – can build quickly to a couple of feet high, then you have to slow down to 3D print rates.
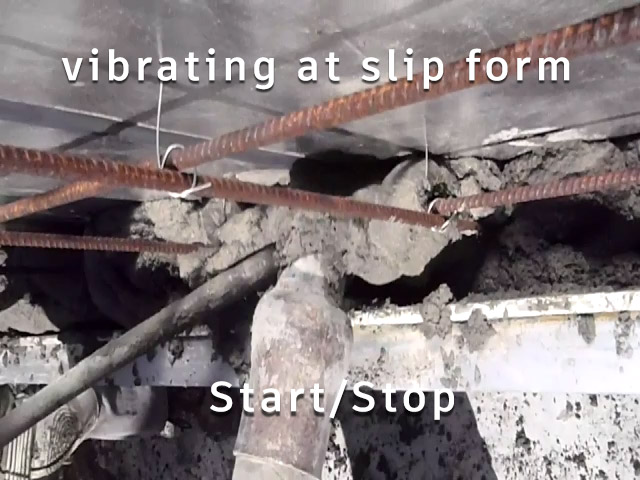
Zero slump with extreme shear thinning, the modified
concrete consolidates very well with vibration.
3D-Admixtm Evolution
The 3D-AdmixTM has evolved from our initial higher-dose system that included a lot of materials that helped the concrete rheology and internal lubricity, but also increased shrinkage and air while reducing strength. We do miss that stuff, because it made it possible for a child to stack concrete one story high in a few minutes, and then retrowel it smooth up to 30 minutes later – in the sun. We are still trying to get those good properties back as much as possible with our present very-low-dose admix system, but without the bad ones. And saving cost by using only mix design materials already present at the batch plant, as much as possible. And we are also testing a 3D-AdmixTM for an extremely-aerated portland-cement mix, that is, a highly 3D-printable very-low-density aircrete.
Alternative Binders
As the 3D-AdmixTM reacts with the presence of more water, particularly with a pH above 8, it provides extreme thickening action with any type of water-reactive cementious mix. Yes, the version we use now is formulated for portland cement concrete, because that is what you can order right now anywhere. But the rheology modification concept is exactly the same for limestone/cement mixes, lime plasters, geopolymers, phosphate cements, ceramics, etc, with the height/rate limitation noted with retarders above – for slow setting binders. The difference for each binder would be the choices for set-accelerators; they would ideally be different types and/or doses, or be omitted altogether where appropriate.
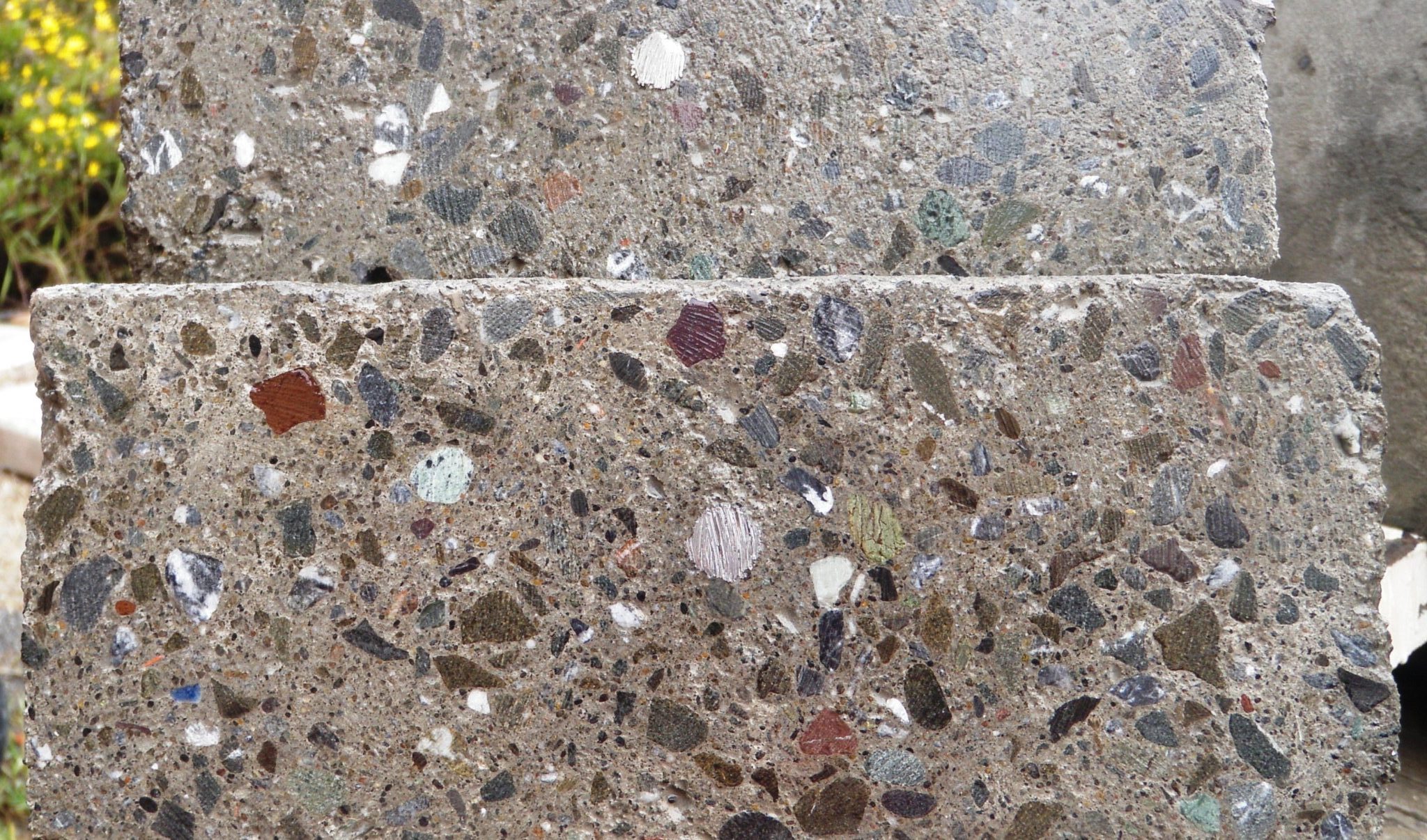